Mielec 2013-10-01
PZL WSK Mielec PZL M-21 Dromader Mini.
261b Section 1982-06-18
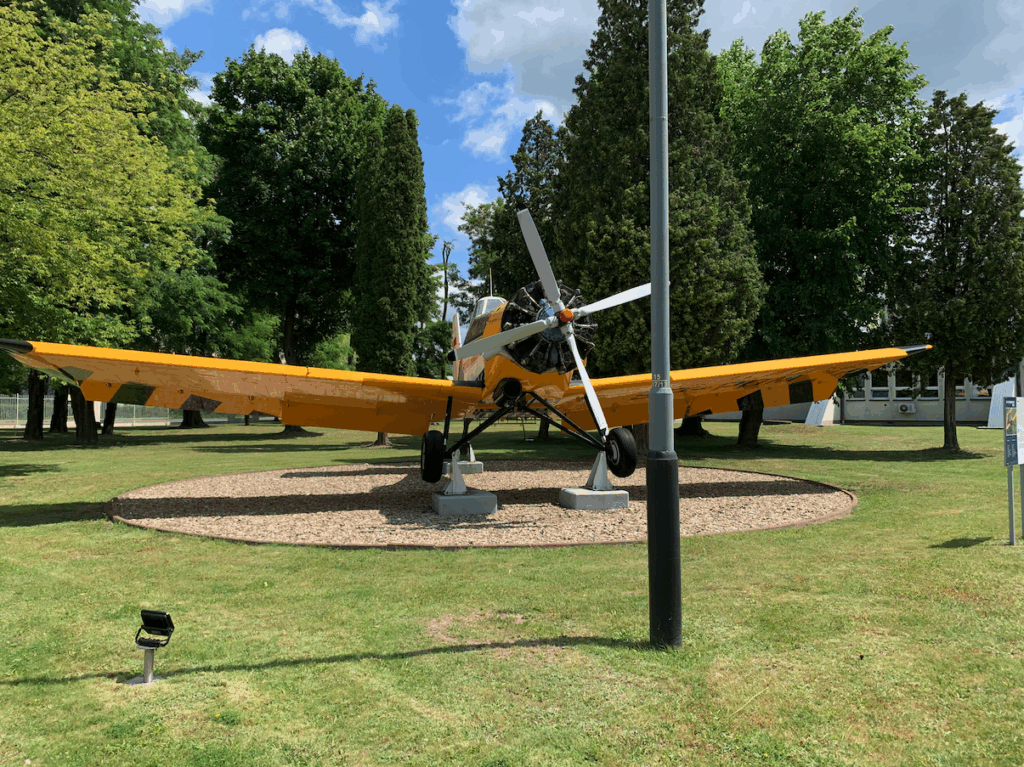
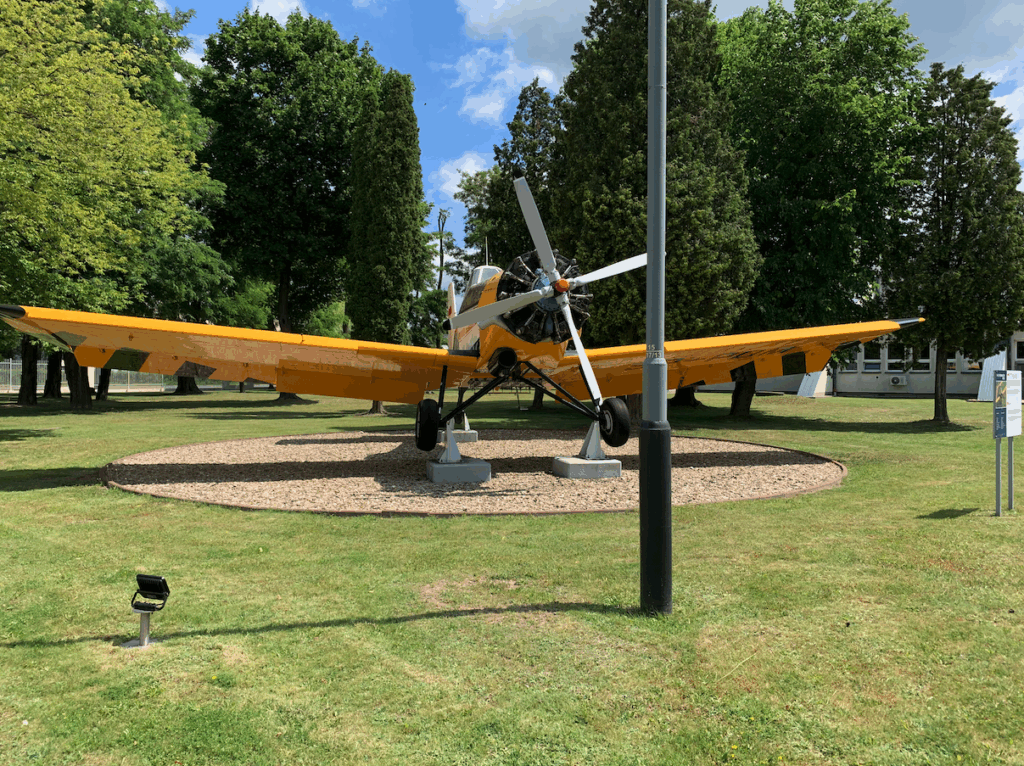
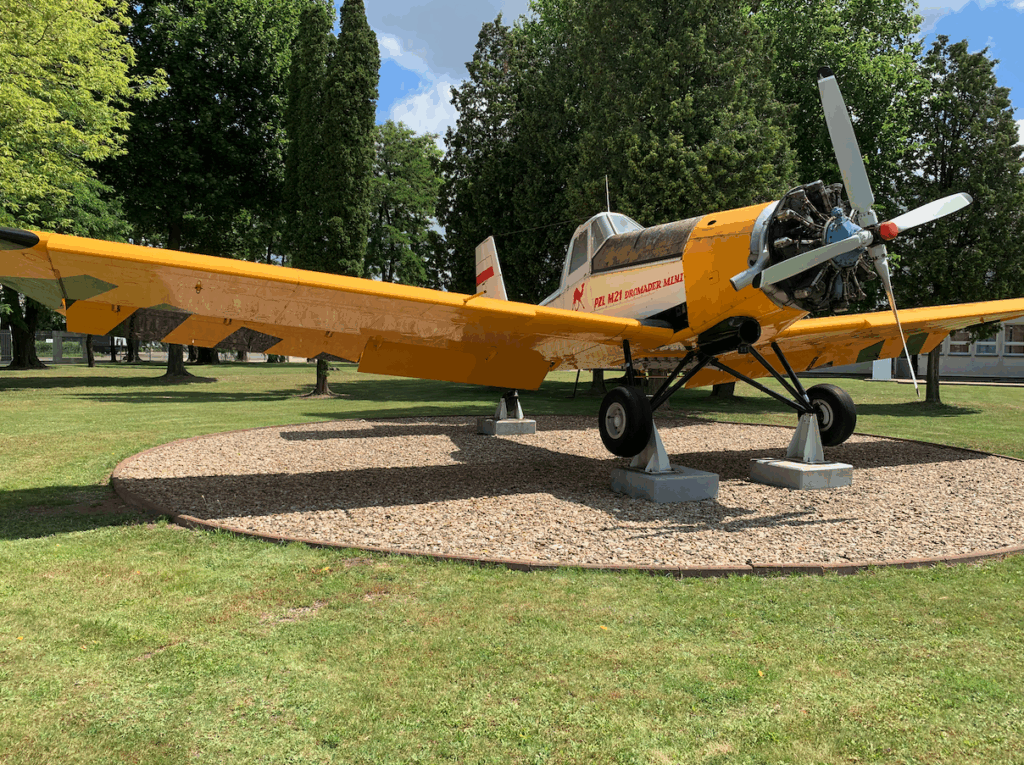
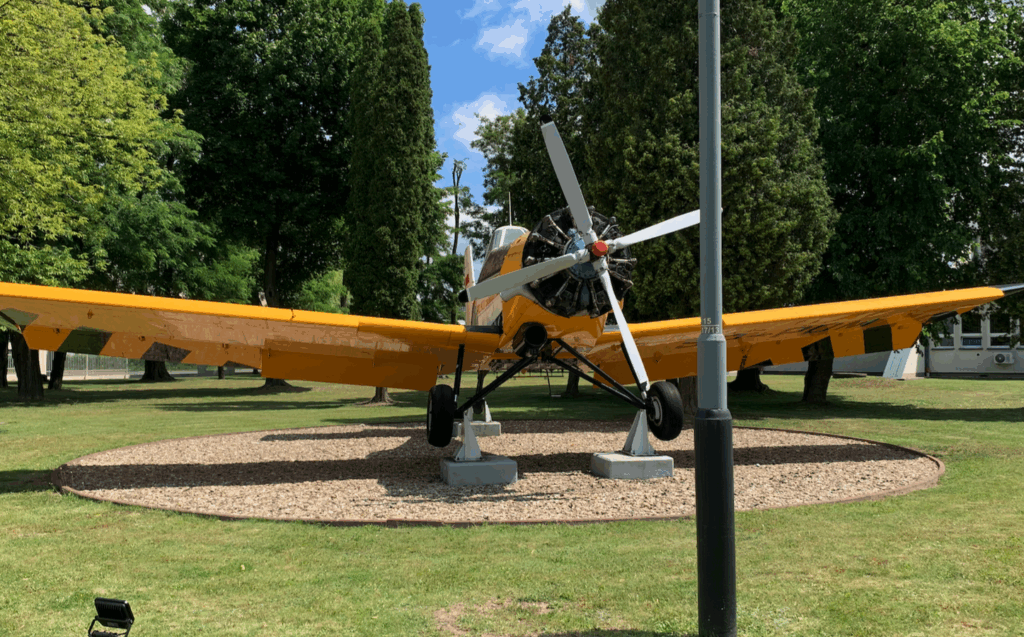
History of the PZL M-21 Dromader Mini.
The PZL M-21 Dromader Mini is an agricultural and firefighting machine. Only two prototypes were built.
The great interest and market success enjoyed by the PZL M-18 Dromader agricultural and firefighting aircraft prompted WSK PZL Mielec to expand its offer. Most users interested in the M-18 Dromader also reported a need for a reduced version of this aircraft, with a lower-power engine and thus lower payload, but structurally unified with the M-18 aircraft. The program received support from state authorities and the Research and Development Center for Communication Equipment at WSK PZL Mielec (formerly known as the Research and Development Company) began work in January 1980. The team was headed by Master of Science in Engineering Jarosław Rumaszewicz. The method of building larger or smaller structures based on the basic aircraft is known and common in the aviation industry around the world. Initial analysis showed that making a reduced version of the M-18 is possible and economically justified. The design of the aircraft, which was designated PZL M-21 Dromader Mini, was started. The basic assumptions were as follows: 441 kW (600 HP) engine. 900 kg tank of chemicals.
It was decided that the drive would be a Polish PZL-3 SR engine with a Polish US-130-000 propeller. This engine is also the basic drive unit of the PZL-106 Kruk agricultural aircraft. The rear part of the fuselage, together with the pilot’s cabin and its equipment, was used from the M-18 aircraft without any major changes. The tail, rear landing gear assembly, and the outer parts of the wings were also taken. Elements of the engine mount, chemical tank, fittings, hydraulic and electrical installations were also used. Equipment for dusting and spraying was also used. As a result, the M-21 aircraft is characterized by a very high degree of unification, amounting to almost 70%. This brings significant benefits, including: shorter design time, smaller scope of research, smaller amount of new documentation, cheaper production and operation. However, there are some disadvantages: greater empty weight of the aircraft, worse performance, greater loads. However, these shortcomings do not significantly affect the entire program and the aircraft is fully competitive with machines of the same size.
The aircraft documentation was completed in June 1980. Two prototypes were built. The first flight was performed on June 18, 1982. At the controls was the chief pilot of PZL Mielec, engineer Tadeusz Pakuła. The aircraft initially had a PZL-3 S engine, and then a PZL-3 SR (441 kW, 600 hp). The second prototype flew in March 1985, SP-PDN, and it was the last prototype.
The aircraft underwent tests in Poland and Yugoslavia (1986-1987). The test results confirmed that the M-21 aircraft is more economical than the M-18 on crops with an area of less than 50 hectares. The aircraft has a take-off weight of 3,300 kg or in a limited version 3,600 kg. It takes 800-1100 kg of chemicals.
In June 1985, the aircraft received a temporary type certificate (without spin tests). Countries such as Nicaragua, Yugoslavia and Bulgaria were interested in the aircraft.
T-T data of the PZL M-21 Dromader Mini aircraft; dimensions wingspan 14.51, length 9.48 m, height 3.82 m, bearing area 38.0 m2. The aircraft has a take-off weight of 3,300 kg or in a limited version 3,600 kg. It takes 800-1100 kg of chemicals. The aircraft has 70% of parts and components from the M-18 aircraft.
The PZL M-21 aircraft did not enter serial production. One of the reasons were the socio-economic changes in the Republic of Poland after 1989 and the liquidation of the Polish Aviation Industry. But there was also another reason. The PZL M-21 Dromader Mini aircraft competed with another Polish design, the PZL-106 Kruk.
The PZL M-21 design.
The aircraft is built in a classic layout, a single-engine low-wing monoplane with a fixed landing gear. Crew; 1 pilot. The aircraft’s service life (at the end of the 80s) was 6,000 hours, which was an excellent result. Permissible overloads of the structure; +3.5 g, -1.4 g. Metal structure. The M-21 design is 70% unified with the M-18 design.
The wing has a NACA 4416 profile at the fuselage and NACA 4412 at the wing tip. The wings consist of three parts: the center wing and two attached wings. The center wing structure is single-spar. Additionally, it has a rear power wall, which is why you can sometimes hear the term – a structure with an auxiliary spar or a double-spar. The center wing covering was made of duralumin sheet metal with a thickness of 0.5 mm to 1.5 mm. Compared to the M-18, the center wing in the M-21 has no flaps. The outer parts of the wings were made using the same technology as the center wing. They are mounted under a slight rise, to move the ends of the wing away from the ground. A pair of flaps and ailerons were mounted on the trailing edge of the outer parts of the wings. Between the main and auxiliary spars, in the outer parts of the wing, there are fuel tanks with a capacity of 2 x 200 liters. All flaps and ailerons were made of metal (aluminum alloys). The spar-rib structure, covered with sheet metal. The ailerons are suspended on ball bearings.
The fuselage of the aircraft is a truss made of chrome-molybdate steel pipes, joined by electric welding in an argon shield. The truss is protected from the outside with epoxy enamels. Internal corrosion protection was provided using oil. The covering was made of duralumin sheets. A partition made of fireproof sheet metal (heat-resistant steel) was permanently mounted at the front of the truss. The engine bed is attached to it. The laminated tank is mounted in the front part of the truss using six fittings. The truss has another eight fittings in the lower part that secure the center wing. The cabin frame is an integral part of the truss. It has been tested for possible capsizing. The cabin accommodates the pilot and a small luggage compartment. The cabin is glazed with organic glass. A windshield consisting of three windows. The front posts are equipped with guillotines for possible severing of the overhead electrical or telephone line. The cabin is equipped with entrance doors, both on the starboard and port side. The doors open outwards, downwards. In the event of an emergency, there is a possibility of emergency ejection of the doors. The rear part of the truss has fittings for attaching the tail gear and the tail. The fuselage covering is attached to the truss mainly by means of quick-connect locks, screw locks and a small number of screws and bolts. The connections between the individual sheets are sealed with gaskets and other sealing compounds. Classic tail divided into rudders and stabilizers. All-metal. Rudders balanced in mass and aerodynamics. Suspended on ball bearings. The horizontal rudder is equipped with two balancing flaps. Moved electrically from the pilot’s cabin. The construction of all units is spar-ribbed. Smooth or grooved covering. At the top of the vertical tail there is a fitting for a cable connecting with the cabin roof. This is protection against power and telephone wires.
Triple-support landing gear, with a tail wheel, fixed. The main landing gear is of a different design than in the M-18. It is attached to the center wing almost under the fuselage, which is why its track is smaller. Main landing gear tires; 800 x 260 mm. Tail wheel tire 360 x 150 mm or 380 x 150 mm. Oil-air shock absorbers. Hydraulic, disc brakes, activated by pedals from the pilot’s cabin. These brakes also function as a parking brake. The tail wheel is self-adjusting, but also equipped with a locking plate, thanks to which we can lock the wheel in the neutral position, from the pilot’s cabin.
The power unit is a PZL-3 SR engine with a power of 1 x 448-544 kW (1 x 600 hp). It is a 7-cylinder, radial engine, air-cooled. Through the reducer, it drives a 3-blade or 4-blade propeller, the blades of which are made of metal. The chemical tank can be used as an additional fuel tank. This requires, however, washing the tank and installing the prepared fuel lines.
Control system consisting mainly of rigid rods and arens (cables in double-acting armour, like gear cables in a bicycle). Hydraulically operated wing flaps. Hydraulic system with working pressure of 10-15 MPa. It deflects the flaps, brakes the chemical pumps with wheels and a fan. Electrical system with a voltage of 24 V. The power source is a 50A/24 V alternator and a 24 V/24 Ah battery. The aircraft has basic flight instruments; artificial horizon, gyro compass, VOR indicator, VHF RS-6102 radio station. It is possible to install other instruments depending on the customer’s wishes.
The chemical tank is designed for bulk substances (powder, granules) or liquids. The tank has a capacity of 1,700 litres. The tank weighs about 100 kg. Its shape resembles a pyramid set with the top down. It has a casing made of glass laminate. The tank is reinforced with two fused steel strips. The tank is connected to the grid with six fittings. The filling opening is placed in the upper part in the form of a hatch that opens outwards. After closing the hatch, it is held by latch locks. The hatch is large enough for a worker to enter to make repairs. Inside, there are two partitions that make it difficult for liquids to flow freely. There are three level scales on the tank, which are visible from the outside and from the pilot’s cabin. The bottom of the tank is a discharge basket, made mainly of stainless steel. A mixer is placed in the basket, which mixes and distributes chemicals. Its side walls have flaps that are adjustable and in this way the amount of dosed agents is regulated. Operating time 3.6 hours.
In addition, the same equipment for dusting, spraying and fogging can be used on the aircraft as on the M-18 and PZL-106 Kruk aircraft.
Data T-T PZL M-21 Dromader Mini:
Wingspan 14.51 m. Length 9.48 m. Height 3.82 m. Gross weight 3,300 kg. Maximum weight 3,600 kg. Payload weight 900 kg. Fuel capacity 404 liters. Maximum speed 230 km/h. Operating speed 155-180 km/h. Cruising speed 227 km/h. Maximum range 700 km. Operating time 3.6 h with 30 min reserve. Ceiling 4,000 m. Take-off run 470 m (at 15 m). Landing run 550 m (from 15 m). Crew 1 pilot.
Written by Karol Placha Hetman