Kraków 2005-03-15
General Dynamics F-16 C/D.
Section 1982-12-14. USA
Multi-role fighter aircraft. Second generation. See the F-16 A/B section.
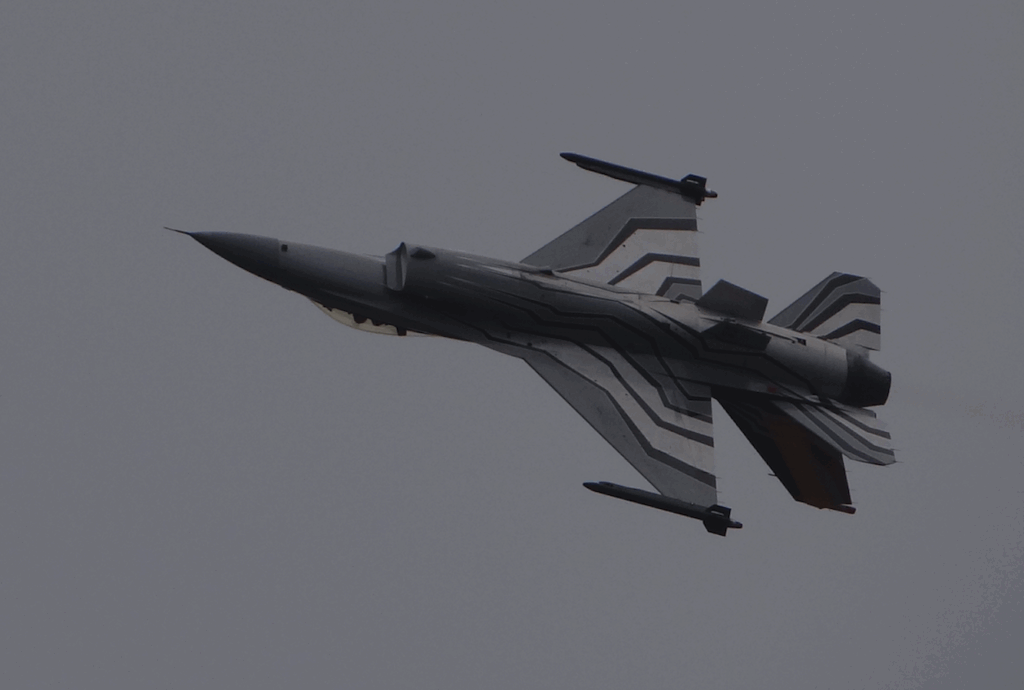
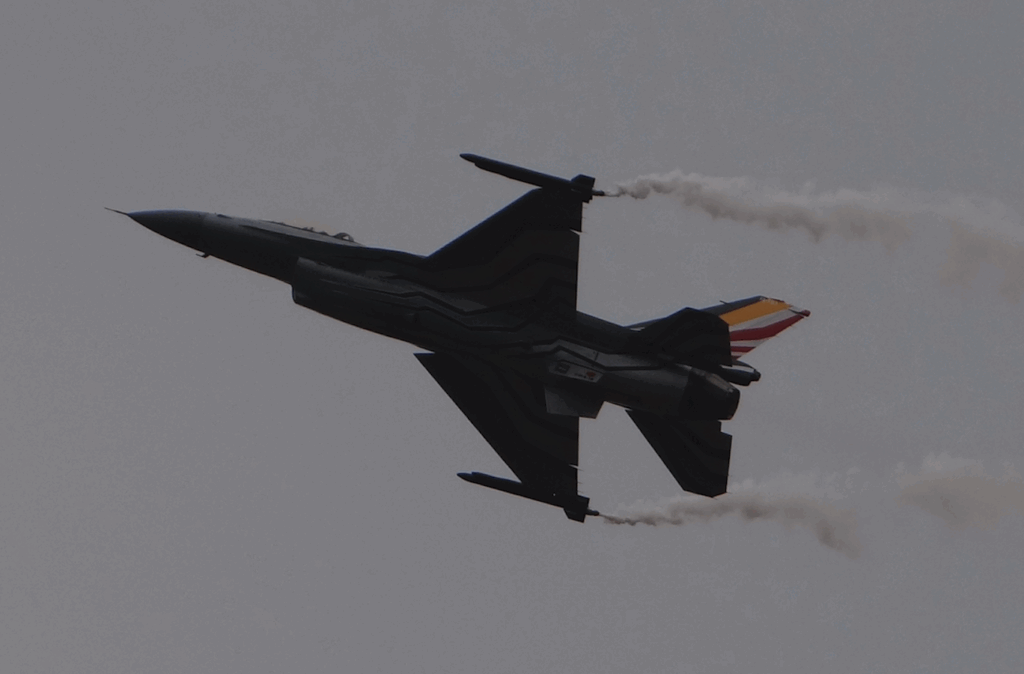
MSIP Modernization.
As early as the late 1970s, F-16 operators were demanding greater combat capabilities. In 1980, a multi-stage F-16 modernization program, designated the Multinational Staged Improvement Program (MSIP), was launched, included within the Enhanced Tactical Fighter (ETF) program. The goal was to achieve a tactical fighter capable of carrying out the most complex combat missions, in all weather and time-of-day conditions, and in complex operational and tactical situations. Due to the complexity of the issues, the MSIP program was divided into three stages, with production still ongoing.
F-16 A/B Block 15/20. 1981. First stage – MSIP-I.
The first phase of MSIP-I was intended for the fourth production series aircraft, 456 designated F-16 A/B Block 15/20, produced from November 1981 to November 1984. These aircraft received new electrical systems to facilitate the subsequent installation of new equipment. The structure of the electronics compartment behind the cockpit was reinforced. An additional fairing was added under the rudder. Norwegian aircraft received a drogue parachute there due to their use on icy airfields. Belgian aircraft received the Loral Rapport III system. The horizontal stabilizer was slightly enlarged again, and its corners were cut to prevent runway contact. The payload capacity of underwings 3 and 7 was increased by 450 kg.
Some aircraft from the fourth production series were produced with further upgrades in accordance with the Operational Capability Update (OCU) program. For example, the Norwegian aircraft were given the ability to carry Penguin anti-ship guided missiles, a radar altimeter, and improved radio navigation equipment.
From 1982 to 1984, the F-16 A/B Block 1/5 aircraft (first and second production series) were upgraded to the F-16 A/B Block 10 standard. From 1987, the F-16 A/B Block 10/15 aircraft (third and fourth production series) were upgraded to the F-16 A/B Block 15 OCU standard.
F-16 C/D Block 20 (new aircraft). 1982.
Major avionics modifications, along with improved weapon loadout capabilities under the MSIP-II/-III programs, led to the introduction of the F-16 C Block 20/25 type of new aircraft. External differences are limited to an extended vertical stabilizer base to accommodate the ASJP jamming system. The aircraft received a new Westinghouse AN/APG-68 radar. A multi-color data display (monitor) and a new head-up display were installed. The first F-16 C aircraft flew on December 14, 1982, and the first F-16 C Block 20, No. 83-118, was delivered to the Army on July 19, 1984. The two-seat version, the F-16 D Block 20, first flew in September 1984.
F-16 C/D Block 25. 1984.
In the MSIP-II phase, the F-16 C/D Block 25 aircraft (fifth production series) were initially developed, starting in July 1984, with the new AN/APG-68 radar, offering nearly double the detection range. The LANTIRN system, a low-altitude navigation system, and the AN/ALR-74 (V) warning receiver were installed. The aircraft had an increased takeoff weight. They were later adapted to carry AMRAAM guided missiles. F-16 C/D Block 25 – the series consisted of 319 aircraft (289 F-16 Cs and 30 F-16 Ds).
F-16 C/D Block 30/32. 1986.
Then, from July 1986, based on the F-16 C/D Block 25, the F-16 C/D Block 30 began to be built, powered by more powerful General Electric F-110-GE-100 engines with one x 72.0 kN of thrust and one x 128.8 kN with afterburning. For reasons, primarily financial, these engines were used by 75% of all aircraft produced. The remaining 25% received modernized Pratt & Whitney F-100-PW-220 engines with one x 65.20 kN of thrust and one x 118.3 kN with afterburning. Aircraft equipped with these engines were designated F-16 C/D Block 32. This duality was subsequently replicated in the subsequent F-16 C/D Block 40/42 and Block 50/52.
Stealth technology, which made it difficult to detect, was introduced for the first time. A refined radar station enabled engagement of multiple targets simultaneously. On-board computer memory was increased, and in 1987, new software was installed. The fuselage fuel tanks received an improved self-sealing system. AIM-120 AMRAAM guided missiles with an active radar seeker were added to the weapon system.
F-16 C/D Block 30 – 408 units produced (360 F-16 C and 48 F-16 D) F-16 C/D Block 32 – 61 units produced (56 F-16 C and 5 F-16 D). Final assembly of the F-16 C/D Block 30 aircraft destined for Turkey was carried out in Turkey.
F-16 N, TF-16 N. 1987.
The U.S. Navy received 26 F-16 N aircraft between 1987 and 1988 to serve as enemy aircraft during pilot training. Four aircraft were built in the two-seat version, designated TF-16 N. The F-16 N and TF-16 N aircraft are equivalent to the sixth production series F-16 C/D Block 30, but are powered by F-110 GE-100 engines. Several other changes were also made to these aircraft. The wing structure was locally strengthened, using titanium instead of duralumin. The aircraft were stripped of their cannon armament. The less powerful AN/APG-66 radar was installed instead of the AN/APG-68.
F-16 C/D Block 40/42 Night Falcon. 1988.
This aircraft, in 1988, became the embodiment of the MSIP-III phase. It became specialized in striking ground targets during day and night, in adverse weather conditions (fog, rain). For this purpose, the aircraft received a LANTIRN targeting and navigation pod and an expanded set of combat assets.
The most important change, enabling attacking ground targets in all conditions, was the use of LANTIRN (Low Level Navigation and Targeting by Infrared for Night) pods, developed since the early 1980s. Testing of the pod began in 1983 and continued until 1988. Initially, due to high cost and delivery priorities, the pods were used in the F-15E Strike Eagle, and in late 1988, LANTIRN pods were deployed in the F-16 C/D.
The system consists of two pods: an AN/AAQ-13 navigation pod and an AN/AAQ-14 targeting pod. The navigation pod houses a Terrain Following Radar (TFR) radar, which, when coupled to the aircraft’s control system, enables flight in accordance with terrain contours at altitudes ranging from 300 to 30 meters. In addition to the TFR radar, the navigation pod contains a thermal imaging camera for monitoring the area ahead of the aircraft, which displays images on the HUD (in the F-16D’s rear cockpit, this image is repeated on one of the CRT monitors – a HUD repeater). A new HUD from GEC Marconi is used, featuring a significantly larger 30-degree x 20-degree field of view. The Block 40 and 42 aircraft are the only variants equipped with this type of HUD. The AN/AAQ-14 targeting pod, with its rotating head, also houses a thermal imaging camera with a variable field of view, but with higher resolution. The pod also houses a laser rangefinder coupled to the camera, illuminating targets. On the F-16 C and F-16 D, the navigation pod is suspended from a node on the left side of the air intake, while the targeting pod is suspended from the right (nodes 5L and 5R), unlike on the F-15 E. The LANTIRN system allowed the full utilization of the AGM-65 D/G missiles. Targets detected and identified using LANTIRN can be designated for earlier AGM-65 missiles. Thanks to the LANTIRN system, the range of weapons carried has also been expanded to include the Paveway family of guided bombs – GBU-10/12/24. Previously, F-16s could drop GBU-10/12 guided bombs, but targets had to be designated and illuminated from another aircraft or ground station.
The radar station was upgraded to the AN/APG-68(V) version, enabling the launch of AIM-120 AMRAAM air-to-air missiles simultaneously at four targets (two at rapid succession). The AN/APG-68(V) had been installed earlier on the F-16 C Block 30, but Block 40 aircraft were the first to be equipped with AIM-120 missiles and were the first to fully utilize the new capabilities.
Changes also affected the airframe. Due to the increased maximum takeoff weight (MTOW) of 19,187 kg (40,000 lbs), the airframe and landing gear were reinforced accordingly. The wheels were slightly enlarged, resulting in characteristic “bubbles” appearing on the main landing gear fairings. Furthermore, it was discovered that the LANTIRN pods partially obscured the taxiing light located on the main landing gear strut. Therefore, it was moved to the nose landing gear fairing. Despite the increased weight, the F-16’s operational limitations remained unchanged.
The first F-16 C Block 40 (87-0350) first flew at Fort Worth on December 23, 1988, and the F-16 D Block 40 followed on February 8, 1989. Aircraft of this version entered USAF service in December 1988. By 1995, a total of 235 ( 234 ) F-16 C Block 40s and 31 F-16 D Block 40s were produced. A total of 462 machines were built in the USA. By 2000, a total of 329 F-16 Cs and 84 F-16 D Block 40s had been produced in Fort Worth. An additional 136 F-16 Cs and 27 F-16 D Block 40s were built at the Turkish TAI plant, of which 34 F-16 Cs and 12 F-16 D Block 40s were delivered to Egypt, and the remaining to the Turkish Air Force. Total production totaled 465 F-16 C Block 40s and 111 F-16 D Block 40s (a total of 576 aircraft), and 149 F-16 C Block 42s and 47 F-16 D Block 42s (a total of 196 aircraft). A total of 772 F-16 C/D Block 40/42s.
In the 1990s, the USAF unofficially designated the Block 40/42 aircraft as F-16 CG and F-16 DG to distinguish their combat capabilities from other F-16 C/D versions. The name Night Falcon is also used to reflect the aircraft’s intended purpose.
F-16 C/D Users
Egypt 1982 – In June 1980, this country signed an agreement for the supply of 34 F-16 A Block 15 and 6 F-16 B Block 15 aircraft. The first aircraft were built in January 1982. The aircraft were delivered between 1982 and 1984. Subsequently, another 40 (45) F-16 C/D Block 32 aircraft were ordered. The first aircraft from this batch was delivered on October 11, 1986. Another agreement was signed in October 1987 for the supply of 47 (42) F-16 C/D Block 40 aircraft with AIM-7 Sparrow missiles. The fourth agreement was signed in June 1990 for the supply of 46 F-16 C/D Block 40 aircraft. In 2000, Egypt had approximately 175 F-16 fighters in service.
South Korea 1986 – First delivery since March 1986: 36 F-16 C/D Block 32 aircraft (30/10). On December 20, 1989, the country decided to purchase 120 F-16 C/D Block 32s. However, the problem was the rising cost of the loan for the F-16s already received. The government was forced to purchase another 120 F-16 C/D Block 52 aircraft with F-100 PW-229 engines. Korea fared well; 12 aircraft were built in the US, but 36 were built from kits supplied to Korea, and 72 were built entirely under license.
Turkey 1987 – In September 1983, Turkey announced its intention to purchase 132 F-16 Cs and 28 F-16 Ds, for a total of 160 aircraft. The first two F-16 C/D Block 30 aircraft were delivered to Turkey in March 1985. Their first flight took place on October 20, 1987. The first 44 aircraft were built as F-16 C/D Block 30 aircraft, followed by Block 40 aircraft with the option of adapting to Block 50. All aircraft are equipped with F-110 GE-100 engines. The order was later increased to 240 F-16 C/D aircraft. Currently (2025), Turkey has approximately 240–250 F-16 aircraft in service, making it the second largest operator of these aircraft in NATO after the USAF.
Greece 1989 – Initial plans for the acquisition of 40 F-16 A/B aircraft to replace the F-5s were made in November 1984. The final contract for the acquisition of 36 F-16 C Block 40s and six F-16 D Block 40s was signed in January 1987. Deliveries lasted from January 1989 to October 1989. A second contract for the delivery of 32 F-16 C Block 50s and eight F-16 D Block 50s was completed between 1997 and 1998. Greece has a total of 170 F-16s delivered under the “Peace Xenia” program between 1989 and 2010, including the Block 30, 50, 52+, and 52+ Advanced versions.
Bahrain 1990 – The country ordered the aircraft in 1987. Deliveries of 18 F-16 C Block 40 and four F-16 D Block 40 aircraft began in March 1990. The aircraft were delivered under two contracts, each for 12 and 10 aircraft. The aircraft participated in the First Iraq War. Currently (2025), Bahrain operates 16-17 F-16 C/D Block 40 aircraft and is taking delivery of 16 new F-16 V Block 70 aircraft.
Other users are discussed in the chapter on the F-16 A/B.
F-16 C/D Design
A single- or two-seat, single-engine, medium-wing aircraft. Multi-role aircraft with enhanced ground attack capabilities, including at night. Designed to withstand +9g and -3g forces.
The wings are trapezoidal in planform, NACA 64A-204 profile, with a 40-degree leading edge sweep, and no lift. The wing aspect ratio is 3.2° and the wing area is 27.87 m². The structure is a multi-spar, two-piece, semi-monocoque, fail-safe design. It consists of 11 spars and eight split ribs, including four reinforced ribs to which the hardpoints are mounted. The spars terminate with milled flanged fittings for attaching the wings to the fuselage. The wing skin is made of single sheet metal. The wing interior is used for fuel tanks. The leading edge features sandwich-type flaps with a honeycomb filler, each with an area of 3.41 m². The trailing edge features flaperons and ailerons, also sandwich-type with a honeycomb filler. These span 80% of the wing’s span and are interchangeable. Both have an area of 2.91 m².
The fuselage is of a modular, semi-monocoque, metal, fail-safe design. The fuselage is partially load-bearing, so when we talk about the wing-like wings of this structure, we’re referring to the side sections of the fuselage capable of generating lift. It’s technologically divided into three sections and an air intake module. The forward section houses the radar station, pilot’s cabin(s), forward fuel tank, and cannon with ammunition drum. The middle module consists of 24 stringers and 8 power frames. The landing gear and landing gear bays are attached to this section. The interior also houses an air duct and fuel tanks, and the dorsal section houses a device for in-flight refueling. The rear section of the fuselage consists of two side booms terminated with crocodile-type brake flaps, with a maximum deflection of 60 degrees. The booms are connected to the engine’s top and are reinforced with lower reinforcements, which also hold the landing hook.
The cabin is air-conditioned and sealed. The instrument panel is equipped with three screens (cathode ray tube monitors) supplemented by a head-up display. Traditional instruments have been reduced to a minimum and serve as emergency controls. Equipment requiring air conditioning is located below the instrument panel. The Aces II 0-0 ejection seat reclines to 30° to improve the pilot’s G-force tolerance. The cabin glazing is made of a single sheet of 14-layer polycarbonate. The fairing lifts upwards and backwards. A small rear window complements the glazing. Visibility is excellent at 360 degrees horizontally and 270 degrees vertically. In the cabin, a joystick is mounted on the right armrest instead of the central joystick.
The tail is a classic design. The vertical tail is swept at 45 degrees, with an area of 5.09 m², and features a four-spar, semi-monocoque structure. The skin is made of carbon composite. The leading edge is a sandwich-type structure with honeycomb filler. The rudder is sandwich-type composite with honeycomb filler, suspended at three points, and has an area of 1.08 m². The rudder controls and some equipment are mounted in the tailplane base. The horizontal tail is a plate-shaped, trapezoidal structure with truncated tips, with a 40-degree sweep and a 10-degree negative lift. Structurally, it consists of a single titanium spar and a duralumin auxiliary spar. The remainder is made of cellular filling and composite sandwich skin. The horizontal tail is interconvertible. The span of the horizontal tail is 5.60 m, and the area is larger than in the A/B versions – 5.92 m². The tail is complemented by two trapezoidal aerodynamic vanes, each set 10 degrees to the sides. The composite structure is cellular.
The landing gear is a three-spoke, single-wheel, retractable landing gear. The front landing gear is mounted on a half-fork, with rearward retractable steering. Dimensions: 0.457 x 0.145 mm, with a pressure of 2.07–2.14 MPa. The main landing gear features disc brakes with an anti-skid system (ABS), which retract forward and rotate 90 degrees to lie flat against the air duct. Dimensions: 0.705 x 0.222 mm, with a pressure of 1.45–1.52 MPa. Oil-gas shock absorbers are located in the legs. The landing gear base is 4.00 m, and the wheelbase is 2.36 m.
The F-16 C/D aircraft are powered by two types of engines:
Block X0 – General Electric F-110-GE-100 with 1 x 72.00 kN thrust and 1 x 128.84 kN with afterburner.
Block X2 – Pratt & Whitney F-100-PW-220 with 1 x 65.20 kN thrust and 1 x 118.30 kN with afterburner.
Equipment and enhanced capabilities of the F-16 C/D.
Block 20 1982
- AN/APG-68 radar.
- ASJP jamming system.
- New head-up display.
- Color monitors.
- Block 25 1984
- AN/APG-68 radar with new software, with twice the range of the AN/APG-66 (90 km).
- LANTIRN system.
- Low-altitude navigation system.
- AN/ALR-74 (V) warning receiver.
- Increased gross weight.
- AMRAAM missiles.
Block 30 1986
- New General Electric F-110-GE-100 engine with 1 x 72.0 kN thrust, and 1 x 128.8 kN with afterburner.
- Stealth technology elements, making it difficult to detect.
- The radar allows for engagement of multiple targets simultaneously. Computers with larger capacity and new software. Improved self-sealing system for fuselage tanks.
- Block 32 1986
- Pratt & Whitney F-100-PW-220 engine with 1 x 65.20 kN thrust, and 1 x 118.3 kN with afterburner.
Block 40/42 1988
Increased range of ground target engagement capabilities, including at night and in poor weather conditions.
Improved and refined LANTIRN navigation and targeting system.
New GEC Marconi head-up display.
Full utilization of AGM-65 D/G missile capabilities.
Independent use of Paveway family guided bombs – GBU-10/12/24.
The radar station was upgraded to the AN/APG-68 (V) version, enabling the near-simultaneous launch of four AIM-120 AMRAAM anti-aircraft missiles.
The aircraft’s weight was increased to 19,178 kg and the landing gear was reinforced.
AN/ALE-40 flare and dipole launcher.
Armament
6-barrel General Electric M61A1 20 mm rotary cannon with 511 rounds. Rate of fire: 6,000 rounds/minute.
9 weapon systems with a payload capacity; for maneuvers above 5.5g: 1 x 1,000 kg underfuselage, 2 x 2,041 kg underwing, 2 x 1,992 kg midship, 2 x 318 kg outer, and 2 x 193 kg tail. For maneuvers at 9g, payloads are limited to 1 x 544 kg, 2 x 1,134 kg, 2 x 907 kg, 2 x 204 kg, and 2 x 193 kg.
The aircraft carries the AIM-120 AMRAM anti-aircraft artillery system and, as before, the following: AIM-7 Sparrow and AIM-9 Sidewinder.
AGM-65 A-G, HARM, and other anti-aircraft missiles.
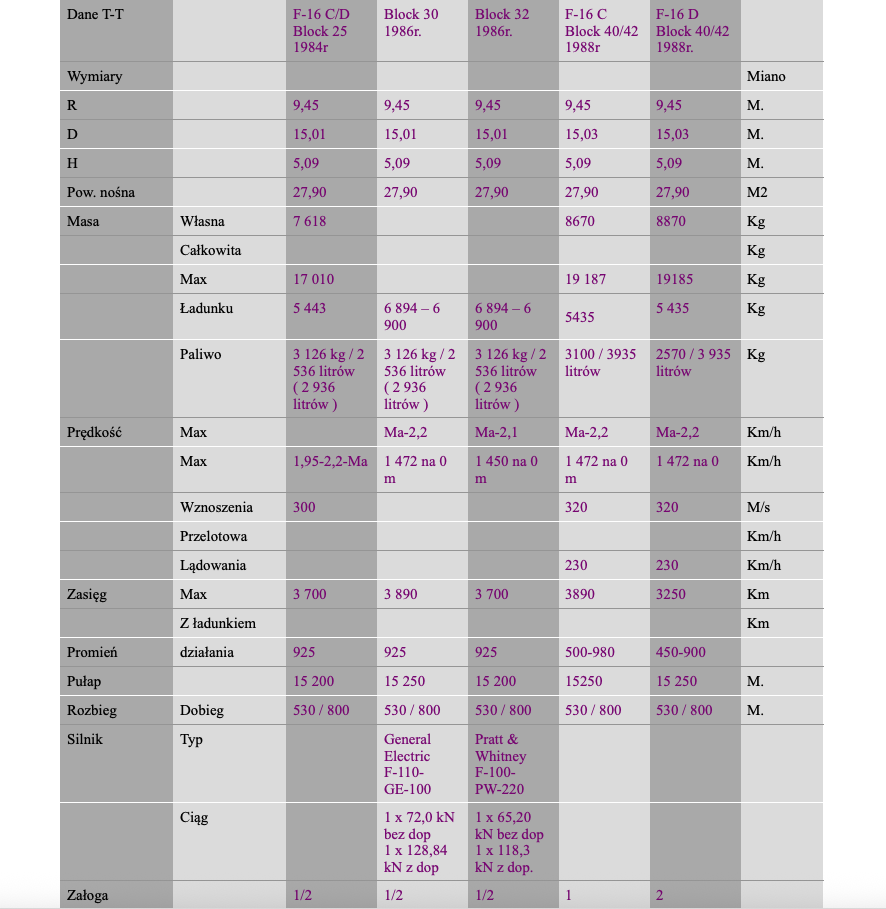
Opracował Karol Placha Hetman